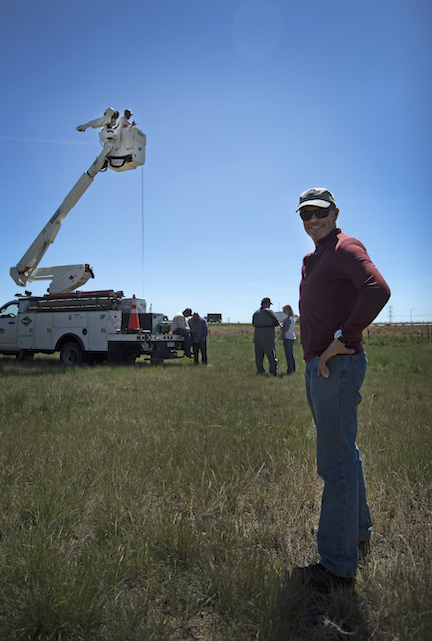
The artist, Douwe Blumberg, conducting site research off Interstate 15 at Exit 365 outside Brigham City in Box Elder County.
This spring all four sides of the spike were welded to the truss tower was successfully rolled out and sandblasted before being rolled back into the studio. A surface neutralizer was then applied to protect the raw aluminum and promote paint adhesion.
The head of the spike was fit and “bodywork” began on the spike shaft. This process is essentially similar to how a car body is worked on using a special two-part putty to fill small holes, imperfections, etc. After the bodywork, the sculpture was primed and prepared for gold-leafing.
A gold-leafing consultant provided intense, hands-on instruction to the team. The consultant is one of the most respected “gilders” in the world and has done work from the U.S. Capitol to the Church of the Holy Sepulcher in Jerusalem. His 42 year career also includes a stint as president of the National Gilders’ Association.
The consultant traveled to the studio and worked with Douwe and his staff for three days on the spike to get the team up to speed on the process. The team has made rapid progress on the gilding process.
This spring and into the summer leafing will happen simultaneously as the spike head is being fitted and finished. When it is finished, the team will apply a two-part protective wax coating and prepare the monument for shipping.
Thank you for your generosity and support of this project. We will continue to update this page as our work progresses.